Prevent PCB Corrosion of Electronics With Anti-Tarnish Vapor Capsules
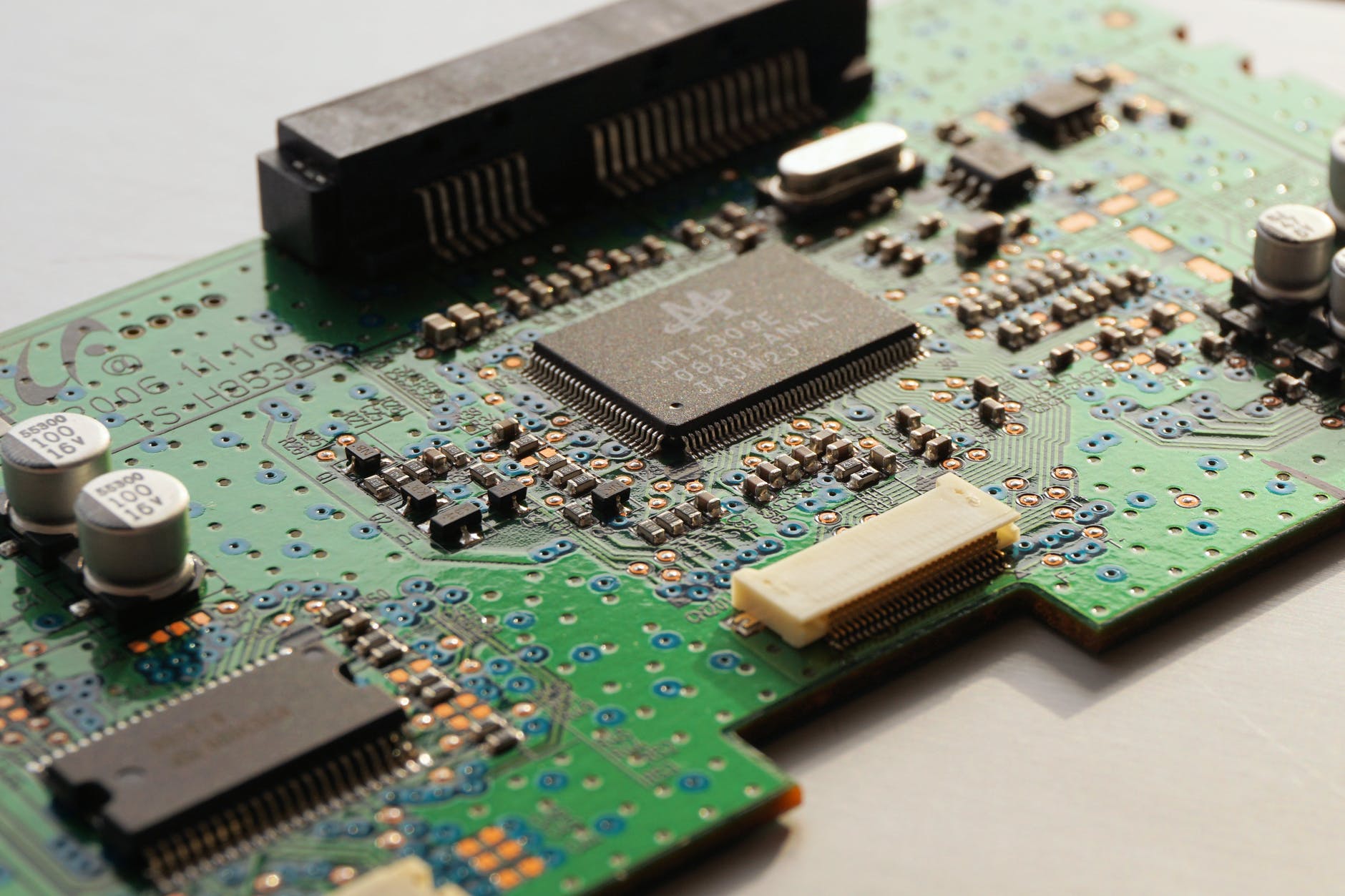
Prevent PCB Corrosion of Electronics With Anti-Tarnish Vapor Capsules
Printed circuit boards, widely known as PCBs, have a broad range of applications, including X-Ray screens, CT scanners, home appliances, entertainment systems, computer systems and smartphones. Because it’s used in so many systems, PCB corrosion of electronics is a major problem for designers, manufacturers, retailers and consumers.
The reality is practically all metallic materials on a PCB are vulnerable to corrosion under certain conditions, particularly if it’s humid. High-performance products may be shielded from the external environment, but this isn’t a full-proof guarantee against PCB corrosion, especially if there are dramatic environmental fluctuations. Corrosion can cause the device to fail. At best, this can be costly. At worst, it can pose safety hazards and even legal liability risks (resulting in the expense incurred for device failure exceeding that of the device itself).
Once a circuit board reaches a certain point of corrosion, it isn’t going to work and it will only get worse. Replacement will be inevitable. But what is corrosion, exactly?
PCB Corrosion Explained
Corrosion is a process that involves oxidation that occurs when oxygen bonds with metal. This can produce rust (if it is a ferrous metal and water/humidity is involved) or other types of corrosion. When corrosion sets in, the metal can flake off and the product can lose valuable chemical properties.
Most printed circuit boards are comprised mostly of metal. Oxygen exposure is practically inevitable. They are likely to corrode at some point. Certain types of metal are more resistant to corrosion. Referred to as “noble metals,” these include copper-nickel alloys, silver, gold and graphite. Conversely, plated tin and nickel, lead and copper (all routinely used in printed circuit boards and other electronic devices) are highly susceptible to corrosion, and are referred to as “base metals.”
PCB corrosion can happen in a few different ways for different reasons. Among the types of corrosion printed circuit boards can experience:
- Atmospheric. This is the most common, with metal being exposed to oxygen and moisture, causing a chemical reaction called oxide. It happens with some metals, like copper, very quickly. If the use of the copper is something like, say, plumbing, this isn’t a huge deal because the product will still retain its mechanical properties. However, if we’re talking about a PCB, it’s a much bigger issue because the product will lose its electrical conductivity.
- Galvanic. This type of corrosion happens when different types of metal come in contact with an electrolyte. Interestingly, those noble metals are actually more susceptible to corrosion than base metals. (Silver, for instance, will corrode rapidly when it comes in contact with tin, which will corrode much more slowly.)
- Electrolytic. This is a type of degradation of metal that occurs when surrounding moisture is contaminated with ions and infects the electrical voltage between two metal pieces, causing a short circuit.
- Fretting. This is a type of where characterized by sliding or oscillation between two pieces of metal (cyclical stresses or vibration). It usually shows up first as pits and grooves and ultimately results in corrosion.
Prevent Printed Circuit Board Corrosion
Technically, you can clean corrosion off a PCB, but it’s preferable to prevent it in the first place if you can. One of the first steps is keeping your PCB cool, dry and clean. Avoid getting liquids or even fingerprints on PCBs. (Product designers should use care not to allow moisture to easily bead up on exposed conductors.)
There are several to ways to reduce the risk of severe PCB corrosion, specifically with vapor corrosion inhibiting products. A number of Zerust VCI products are specifically designed for this purpose. Examples include:
- Anti-tarnish vapor capsules. These capsules are easy-to-use and provide up to one year of protection for any non-ferrous metal compounds sealed in an enclosed area of up to 2 feet. The capsules are equipped with an adhesive backing and can simply be placed on an interior surface.
- Plastabs. These are thin, rigid and light little squares and rectangles that have VCI tech molded into the plastic, offering PCB corrosion prevention. They’re great for protecting hard-to-reach, compact electrical components of printed circuit boards, as well as control boxes and enclosure cabinets. They offer up to two years of protection.
- Toolbox drawer liners. The PVC rubber contains VCI tech and can be cut to size to fit inside drawers, toolboxes or other shelves where electronics or electronic components are stored. These have the added benefit of preventing denting, slipping and mold/mildew, with PCB corrosion protection lasting up to five years.
If you have questions about the best method for protecting your PCBs from corrosion, our Zerust experts are happy to help.
cu*************@ze************.com“>Contact Zerust for information on VCI products to help with electronics corrosion prevention by emailing us or calling (330) 405-1965.
Additional Resources:
Corrosion in electronics: Overview of failures and countermeasures, Jellesen, Morten Stendahl; Verdingovas, Vadimas; Conseil, Helene; Piotrowska, Kamila; Ambat, Rajan, Proceedings of EuroCorr 2014
More Blog Entries:
Shipping Electronics Overseas? Plastabs, Vapor Capsules Offer Electronics Corrosion Prevention, Dec. 19, 2020, Zerust PCB Corrosion Prevention Blog